防止精密鑄造蠟模變形的方法
發(fā)布日期:2022-08-04 00:00 來源:http://gzmmw.cn 點擊:
熔模精密鑄造在生產(chǎn)中較多采用糊狀模料,這主要由于糊狀模料比液態(tài)模料收縮小、凝固快、生產(chǎn)率高。在壓型一蠟模一精密精鑄蠟造件的生產(chǎn)過程中,蠟模的尺寸穩(wěn)定性和變形程度,大大地影響了精密鑄造件的質(zhì)量狀態(tài)。針對易變形件要從頭道工序一射蠟就采用在蠟模中放入阻礙物限制收縮變形,開澆道根后粘澆道,壓蠟后在水中冷卻等有效措施,使蠟模處在一個良好的質(zhì)量狀態(tài)之下。大量生產(chǎn)實踐證明,這些預防措施是有效并且十分必要的。
在蠟模中放入阻礙物限制收縮變形精密鑄造件右頁結(jié)構(gòu),因需保證門的回轉(zhuǎn)良好,故兩個Ф10.5mm的孔要求同軸,客戶要求用銷軸檢具全檢,并且銷軸一端要自由落體式無障礙地穿過兩個孔。原來的生產(chǎn)工藝為:壓蠟后,壓型放入水中冷卻30min后取出蠟模。精密鑄造件用銷軸穿兩個Ф10.5mm的孔,因兩孔不同軸,銷軸穿不進去,需要100%校正,而且變形沒有一點規(guī)律,極大增加了校正工作量,嚴重拖后生產(chǎn)進度。針對此情況,改進了工藝,經(jīng)過計算,做了10根Ф10.80-0.1mm的銷軸,在壓制右頁蠟模后,就將該銷軸在Ф10.5mm孔處穿入蠟模,之后一并放入水中,冷卻30min后取出,針對這些蠟模做了兩種方法:一種是修蠟模后直接組樹,另一種是再在上面粘一條拉筋。精密鑄造件生產(chǎn)出來用銷軸檢測,只有1件兩孔略偏斜,其余則完全符合要求,此1件偏斜的右頁,稍一校正即可符合要求。經(jīng)歸類,發(fā)現(xiàn)第1種方法未粘拉筋的就已經(jīng)滿足生產(chǎn)要求,可投入批量生產(chǎn)。
5×5BT閥套精密鑄造件閥套的4個爪有嚴格要求,爪的外圓要求加工,必須保證足夠的加工量,露黑皮不行。為此,在蠟模和精密鑄造件上均有樣板檢測爪尺寸變化。原來的工藝為:壓蠟后放入水中冷卻40min后取出蠟模。經(jīng)檢測,4爪在蠟模上總體為向內(nèi)變形,每個爪還左右擺,變形沒有規(guī)律。射蠟工1小時只能修出7件符合樣板的蠟模。為解決變形問題,經(jīng)計算,專門制作了金屬支撐圈,雙點劃線所示,在閥套蠟模射出后,將金屬支撐圈插入,一并放入冷水中冷卻40min后取出。在采用金屬支撐圈并按工藝要求校正蠟模后,幾乎不用修蠟模,提高了修蠟模的工作效率。現(xiàn)批量生產(chǎn)中已按改進后工藝執(zhí)行,取得了良好效果。
采用開澆道根后粘澆道的措施DNl50法蘭盤結(jié)構(gòu),其結(jié)構(gòu)對稱、壁厚均勻。如果直接在其上開出澆道,因澆道較厚大,與蠟模本體形成壁厚差,不只在從模具拿出過程中取蠟模困難,而且會因取模方式不當造成變形;也會在蠟模的冷卻過程中因壁厚不均,而造成收縮變形。所以綜上考慮,對DNl50法蘭盤采用先預設澆道根(高度為1.0~1.5mm),后粘澆道的方法來避免在蠟模上因澆道厚大而形成壁厚不均,導致收縮不同步的變形。
蠟模冷卻方式:壓蠟后,還要注意冷卻方式的選擇,通常是在空氣中冷卻或在冷水中冷卻。在冷水中冷卻可強制蠟模定型,而有些三端或兩端為法蘭盤,如DN40法蘭閘閥體,在正常生產(chǎn)條件是放入水箱中冷卻的,導致在蠟模上的兩法蘭盤間距L1和L2相差得很大,可達到2.0~2.5mm。
經(jīng)分析,除結(jié)構(gòu)本身的特點,蠟模在水箱中為漂浮狀態(tài),出現(xiàn)蠟模的一部分在水中,一部分在空氣中的情況。由于水面上下的法蘭盤冷卻條件不同,產(chǎn)生的收縮不同,使法蘭盤產(chǎn)生較大的變形。為防止這種現(xiàn)象,應設法使蠟模完全浸入水中。使同一蠟模的各個部位冷卻條件一致,待尺寸穩(wěn)定后再取出,可減少此類問題的發(fā)生。
在蠟模中放入阻礙物限制收縮變形精密鑄造件右頁結(jié)構(gòu),因需保證門的回轉(zhuǎn)良好,故兩個Ф10.5mm的孔要求同軸,客戶要求用銷軸檢具全檢,并且銷軸一端要自由落體式無障礙地穿過兩個孔。原來的生產(chǎn)工藝為:壓蠟后,壓型放入水中冷卻30min后取出蠟模。精密鑄造件用銷軸穿兩個Ф10.5mm的孔,因兩孔不同軸,銷軸穿不進去,需要100%校正,而且變形沒有一點規(guī)律,極大增加了校正工作量,嚴重拖后生產(chǎn)進度。針對此情況,改進了工藝,經(jīng)過計算,做了10根Ф10.80-0.1mm的銷軸,在壓制右頁蠟模后,就將該銷軸在Ф10.5mm孔處穿入蠟模,之后一并放入水中,冷卻30min后取出,針對這些蠟模做了兩種方法:一種是修蠟模后直接組樹,另一種是再在上面粘一條拉筋。精密鑄造件生產(chǎn)出來用銷軸檢測,只有1件兩孔略偏斜,其余則完全符合要求,此1件偏斜的右頁,稍一校正即可符合要求。經(jīng)歸類,發(fā)現(xiàn)第1種方法未粘拉筋的就已經(jīng)滿足生產(chǎn)要求,可投入批量生產(chǎn)。
5×5BT閥套精密鑄造件閥套的4個爪有嚴格要求,爪的外圓要求加工,必須保證足夠的加工量,露黑皮不行。為此,在蠟模和精密鑄造件上均有樣板檢測爪尺寸變化。原來的工藝為:壓蠟后放入水中冷卻40min后取出蠟模。經(jīng)檢測,4爪在蠟模上總體為向內(nèi)變形,每個爪還左右擺,變形沒有規(guī)律。射蠟工1小時只能修出7件符合樣板的蠟模。為解決變形問題,經(jīng)計算,專門制作了金屬支撐圈,雙點劃線所示,在閥套蠟模射出后,將金屬支撐圈插入,一并放入冷水中冷卻40min后取出。在采用金屬支撐圈并按工藝要求校正蠟模后,幾乎不用修蠟模,提高了修蠟模的工作效率。現(xiàn)批量生產(chǎn)中已按改進后工藝執(zhí)行,取得了良好效果。
采用開澆道根后粘澆道的措施DNl50法蘭盤結(jié)構(gòu),其結(jié)構(gòu)對稱、壁厚均勻。如果直接在其上開出澆道,因澆道較厚大,與蠟模本體形成壁厚差,不只在從模具拿出過程中取蠟模困難,而且會因取模方式不當造成變形;也會在蠟模的冷卻過程中因壁厚不均,而造成收縮變形。所以綜上考慮,對DNl50法蘭盤采用先預設澆道根(高度為1.0~1.5mm),后粘澆道的方法來避免在蠟模上因澆道厚大而形成壁厚不均,導致收縮不同步的變形。
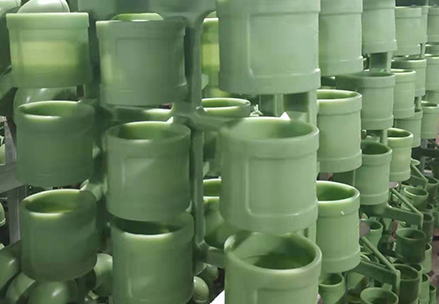
蠟模冷卻方式:壓蠟后,還要注意冷卻方式的選擇,通常是在空氣中冷卻或在冷水中冷卻。在冷水中冷卻可強制蠟模定型,而有些三端或兩端為法蘭盤,如DN40法蘭閘閥體,在正常生產(chǎn)條件是放入水箱中冷卻的,導致在蠟模上的兩法蘭盤間距L1和L2相差得很大,可達到2.0~2.5mm。
經(jīng)分析,除結(jié)構(gòu)本身的特點,蠟模在水箱中為漂浮狀態(tài),出現(xiàn)蠟模的一部分在水中,一部分在空氣中的情況。由于水面上下的法蘭盤冷卻條件不同,產(chǎn)生的收縮不同,使法蘭盤產(chǎn)生較大的變形。為防止這種現(xiàn)象,應設法使蠟模完全浸入水中。使同一蠟模的各個部位冷卻條件一致,待尺寸穩(wěn)定后再取出,可減少此類問題的發(fā)生。